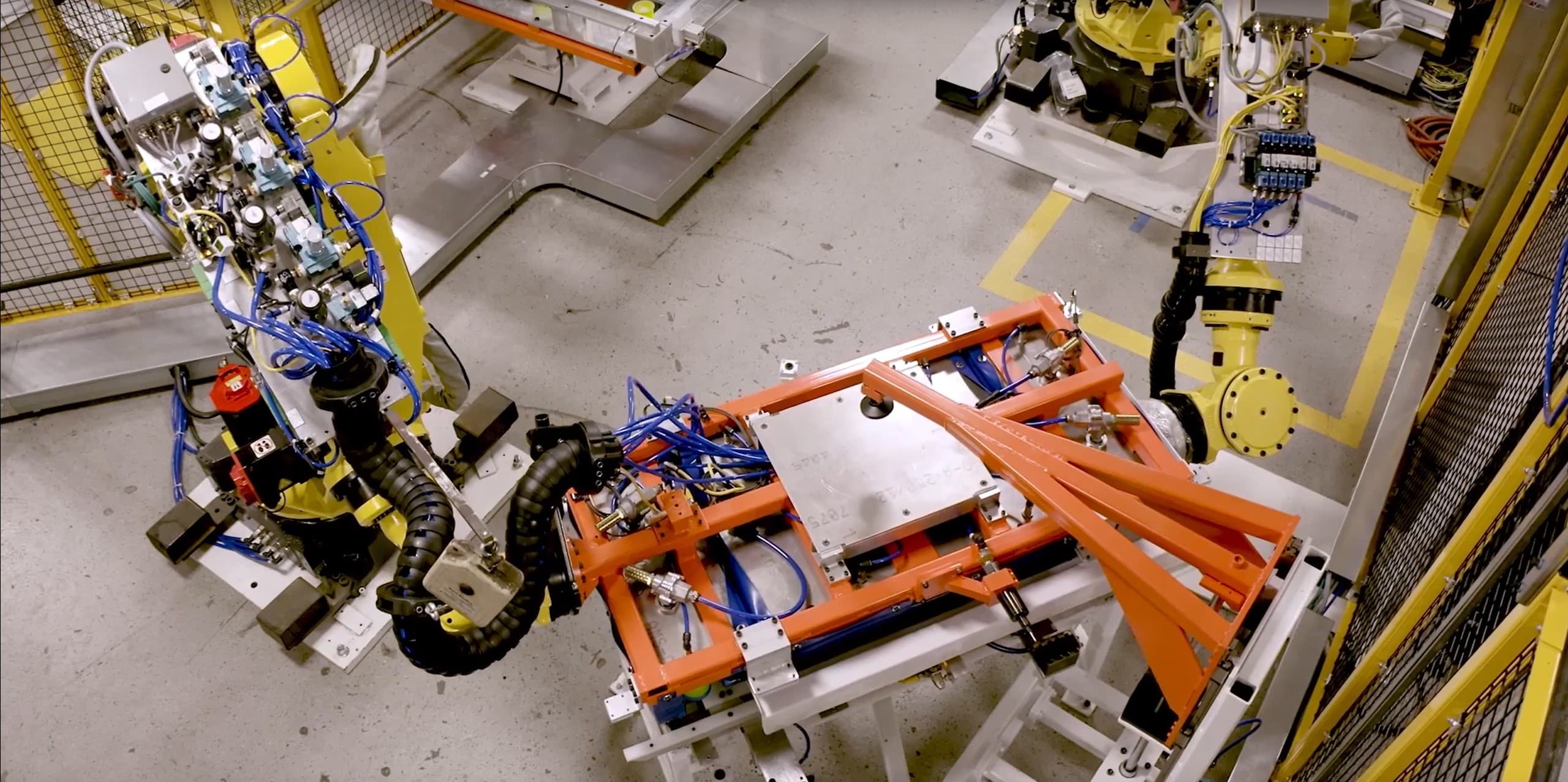
Industrial Automation
Reduce operating costs and free your team to focus on high-value work and innovation.
Work with a cross-functional team to define the problem and openly explore solutions.
We design, build, and deliver turnkey systems and pre-engineered workcells. But just as critical—we handle system integration, modernization, retrofits, upgrades, and process improvements. For any system. Not just the ones we built.
ICR stays committed to the long-term success of your operation. For us, project close is a beginning. After-sales support starts immediately and continues throughout the lifecycle.
Material Handling
Assembly
Dispensing
Palletizing
Machine Vision
Packaging
Welding
Plasma Cutting
Machine Tending
CS-198 Success Story
A FANUC R-2000iC/125L long-arm, heavy-payload robot feeds high-density fuel tanks downstream.



Double-sided EOAT with vacuum end-effector loads and unloads parts from the injection molding machine. The system moves each part to a checkweigher, applies a laser-etched barcode, and updates the MES.
A barcode reader verifies each part before transferring it to storage for post-process cooling.
Phase-gate
Defined deliverables and milestones, an upfront risk matrix, and change management with cost-benefit analysis to align resources and budget.
Concept
Define the problem, align on needs, set requirements, confirm feasibility, and deliver the SOW for project approval.
Design, Fabricate, Validate
2X faster design—Proof of Concept with 3D CAD and simulation. Begin fabrication. Validate with a Factory Acceptance Test, then ship.
Install
Install and complete the Site Acceptance Test, train the team, and introduce Lifecycle Management.
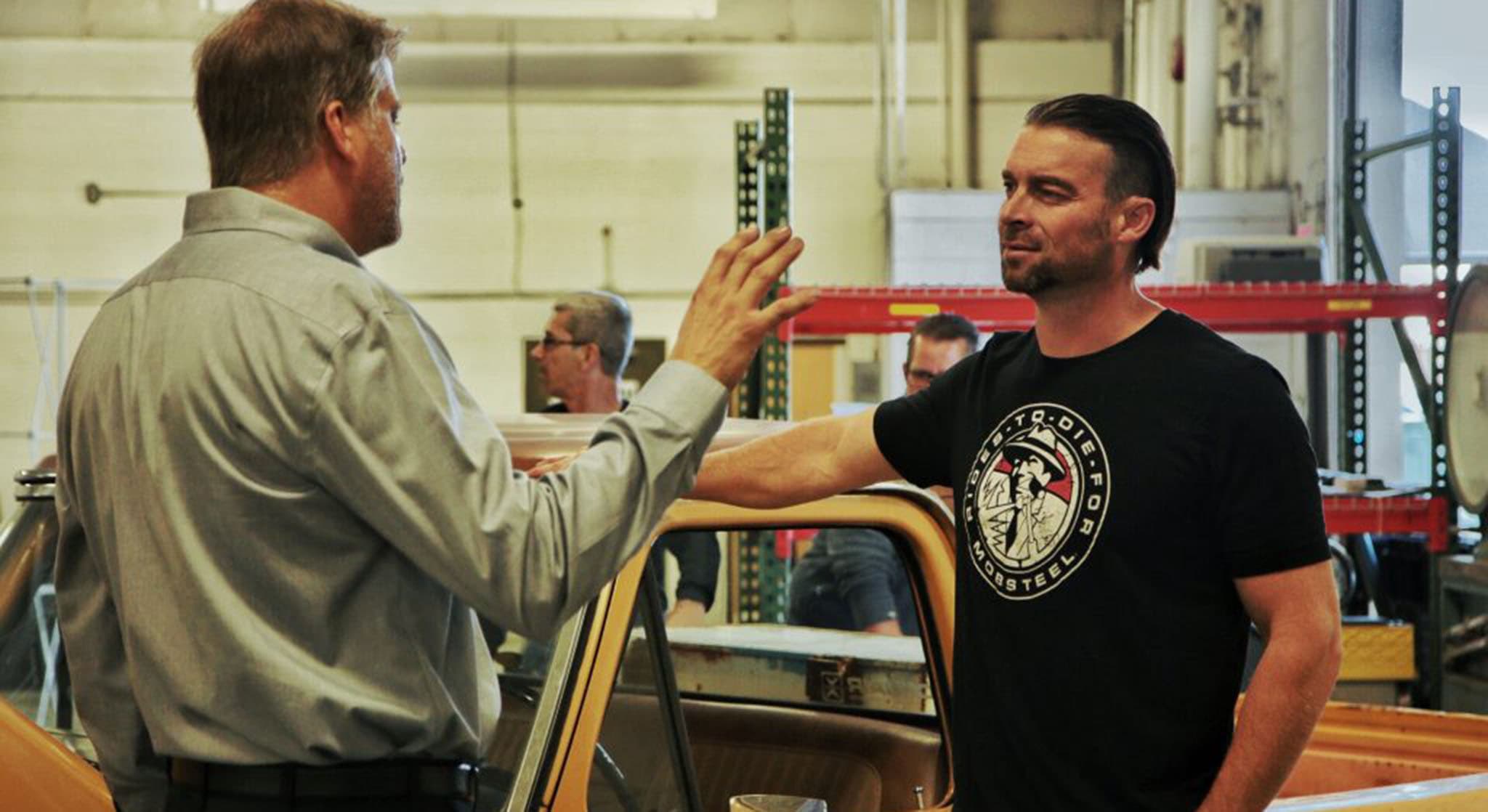
Support
After-sales
Assess system performance, perform post-installation maintenance and repair, and helm continuous improvements.
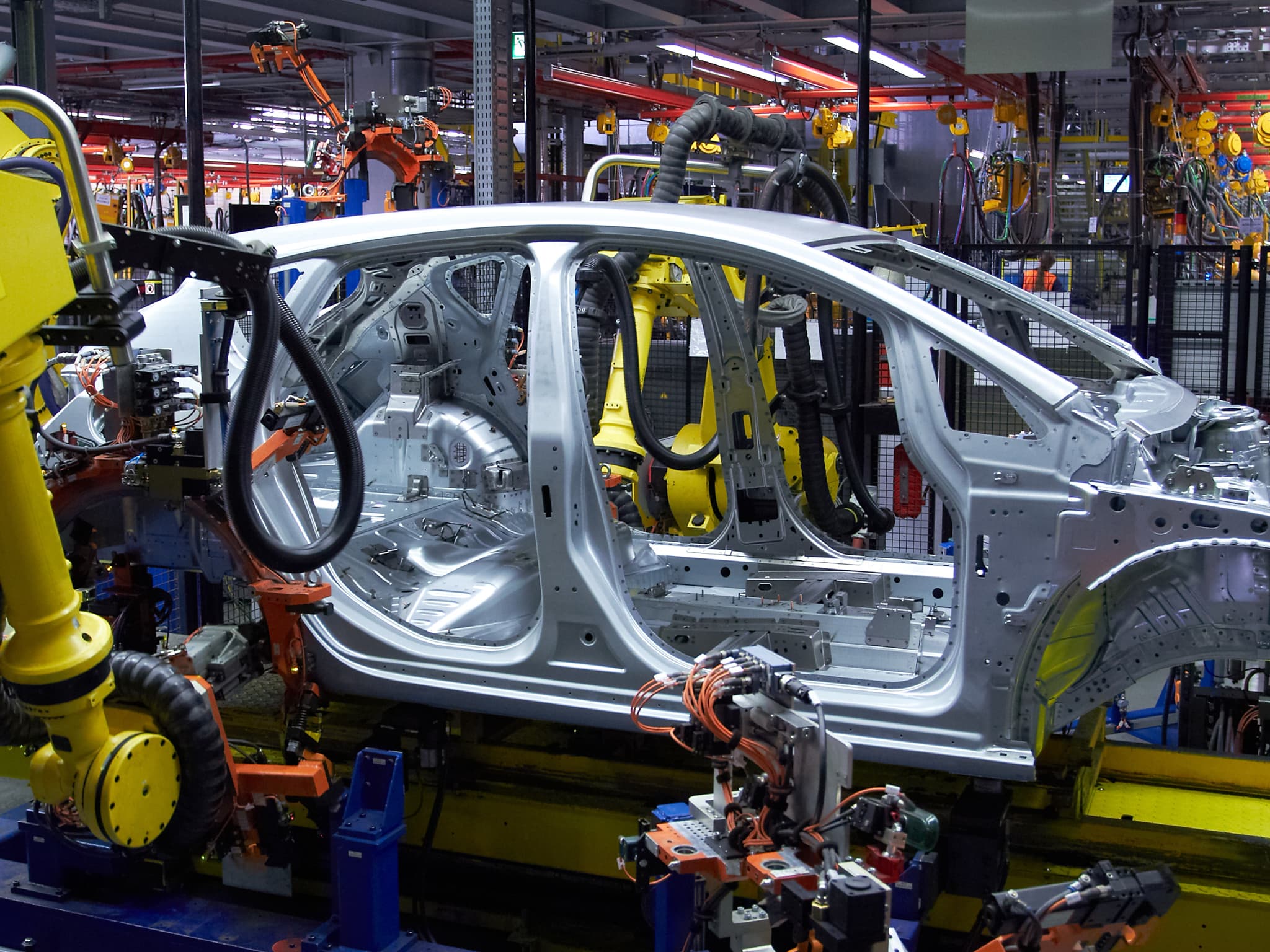
Automotive
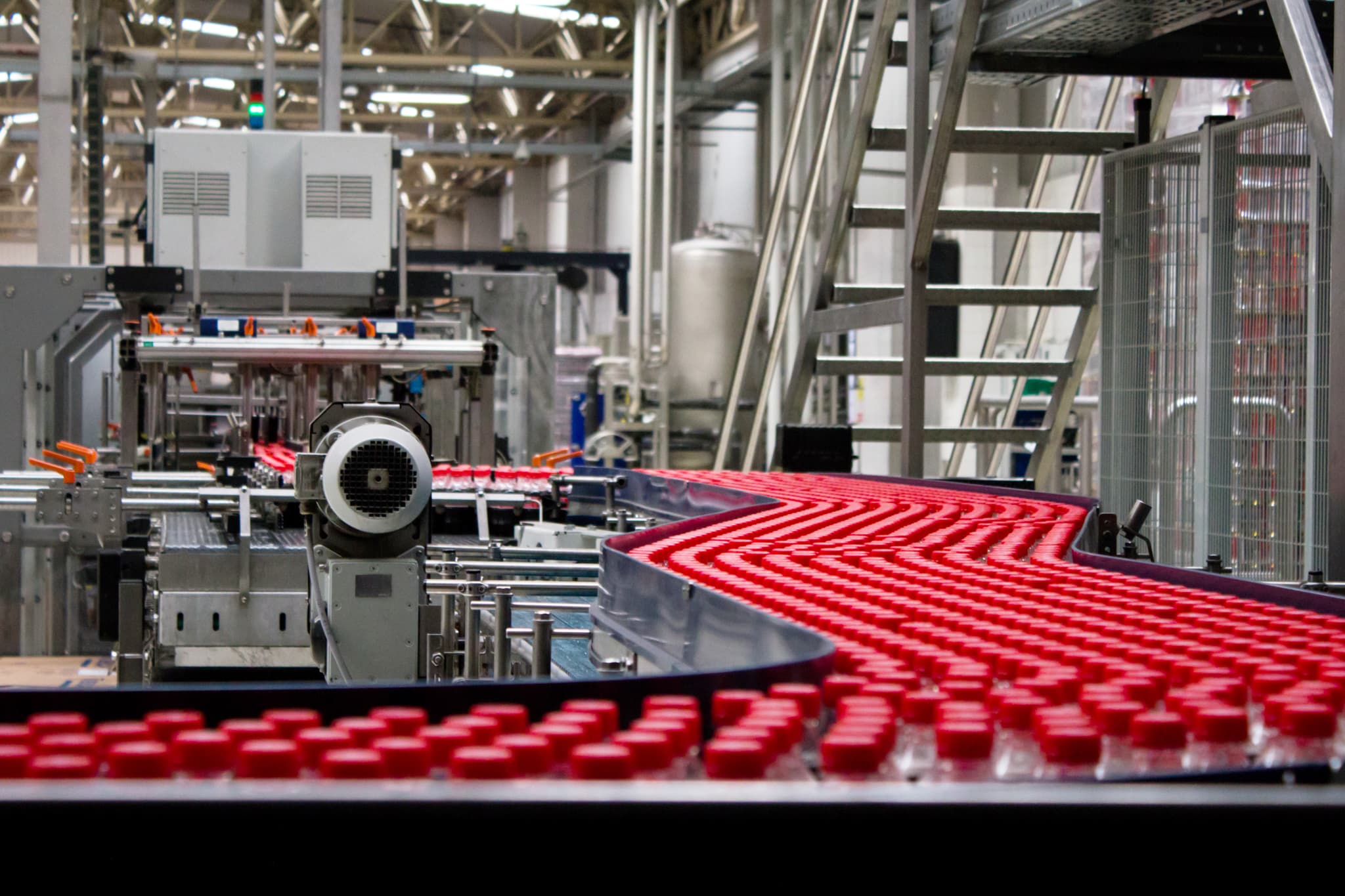
Food and Beverage
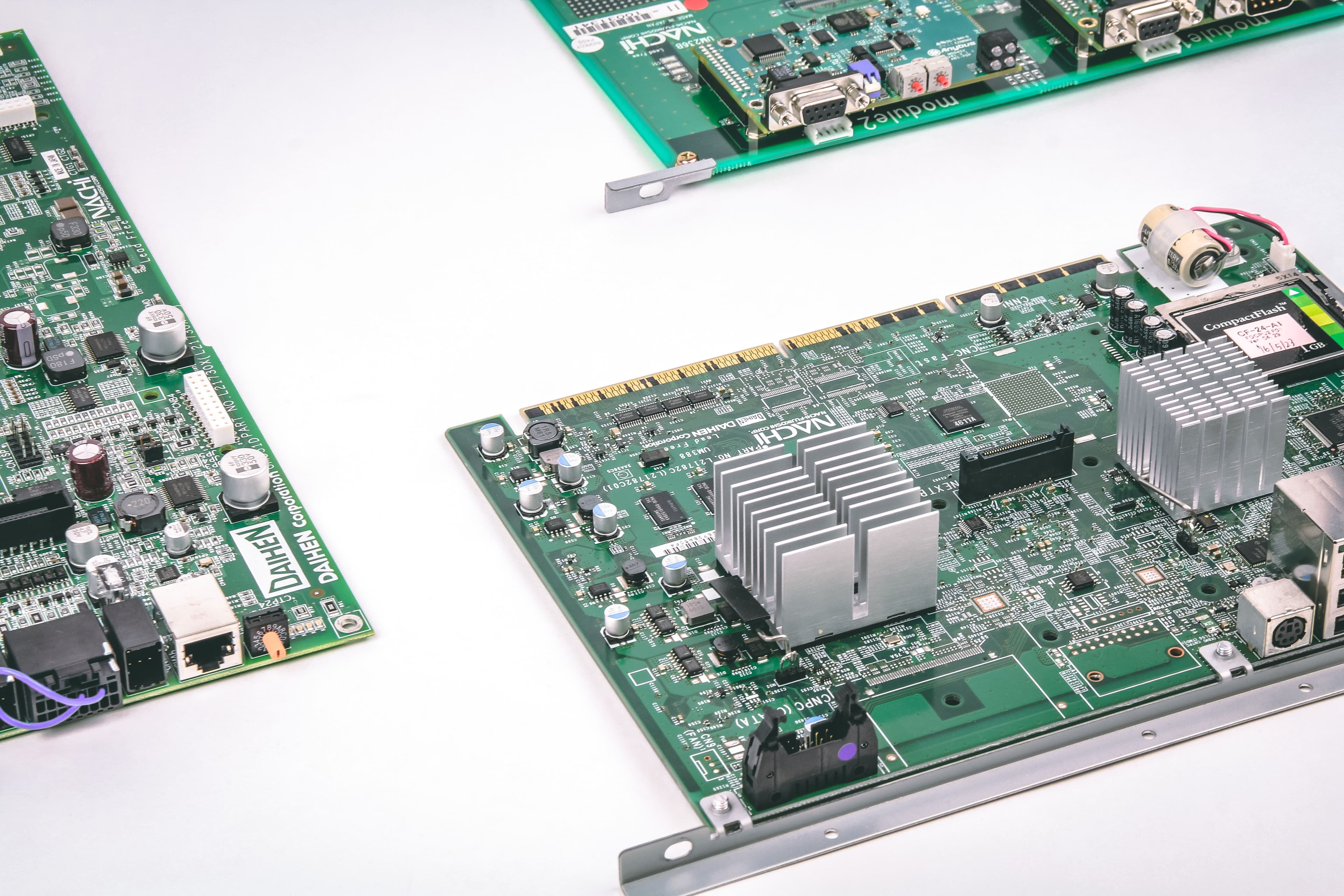
3C Electronics
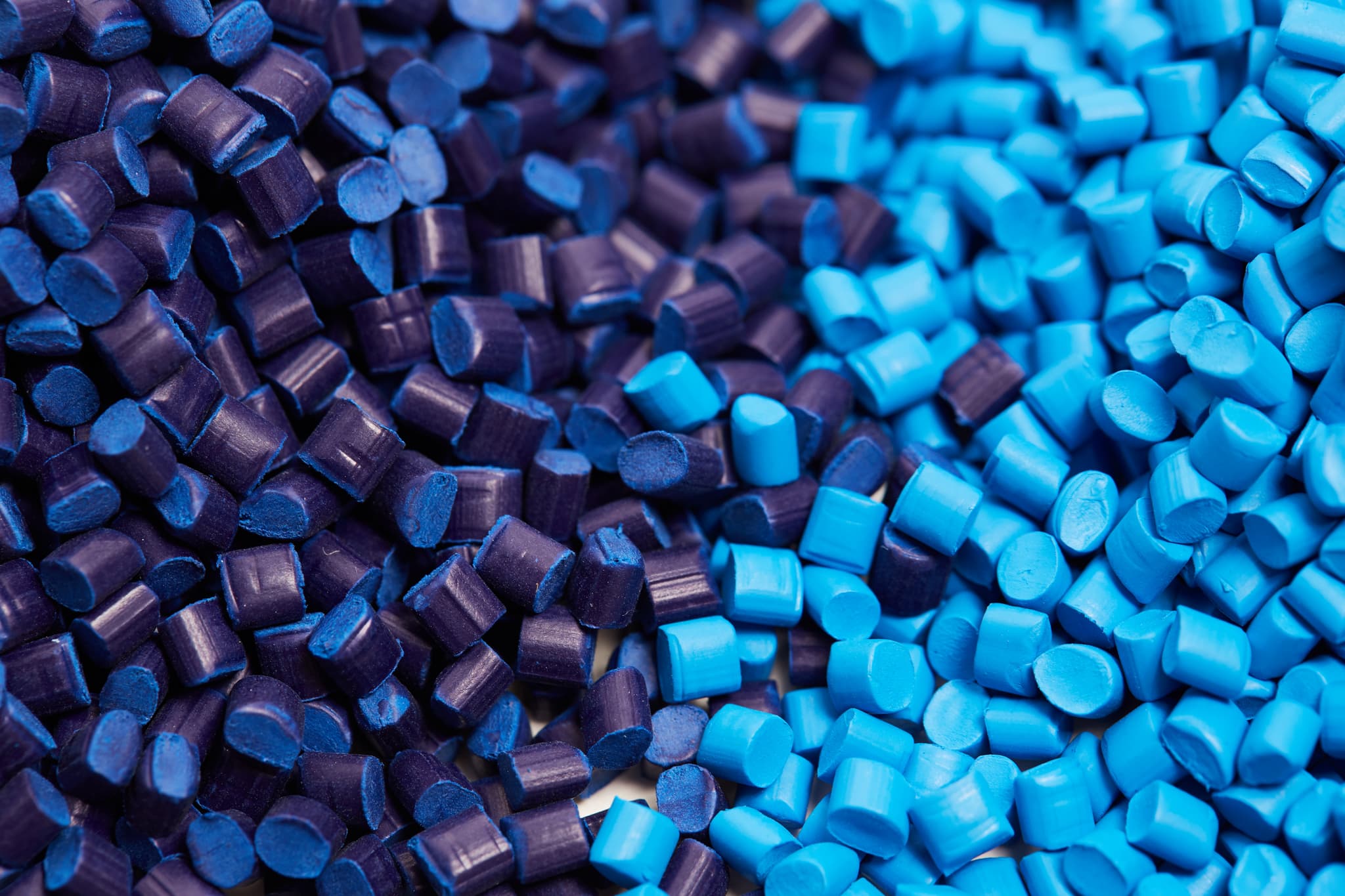
Plastics
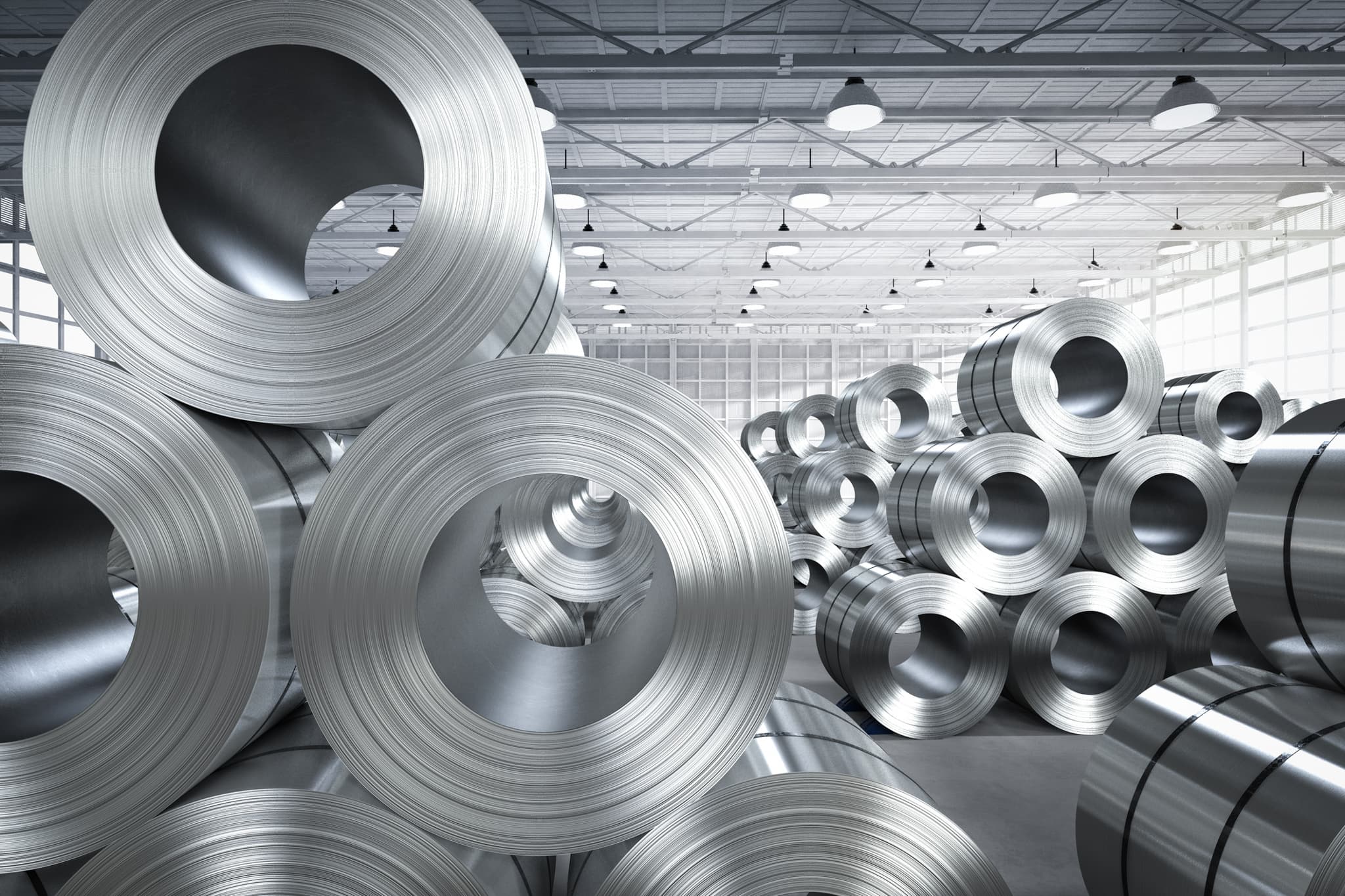
Metals
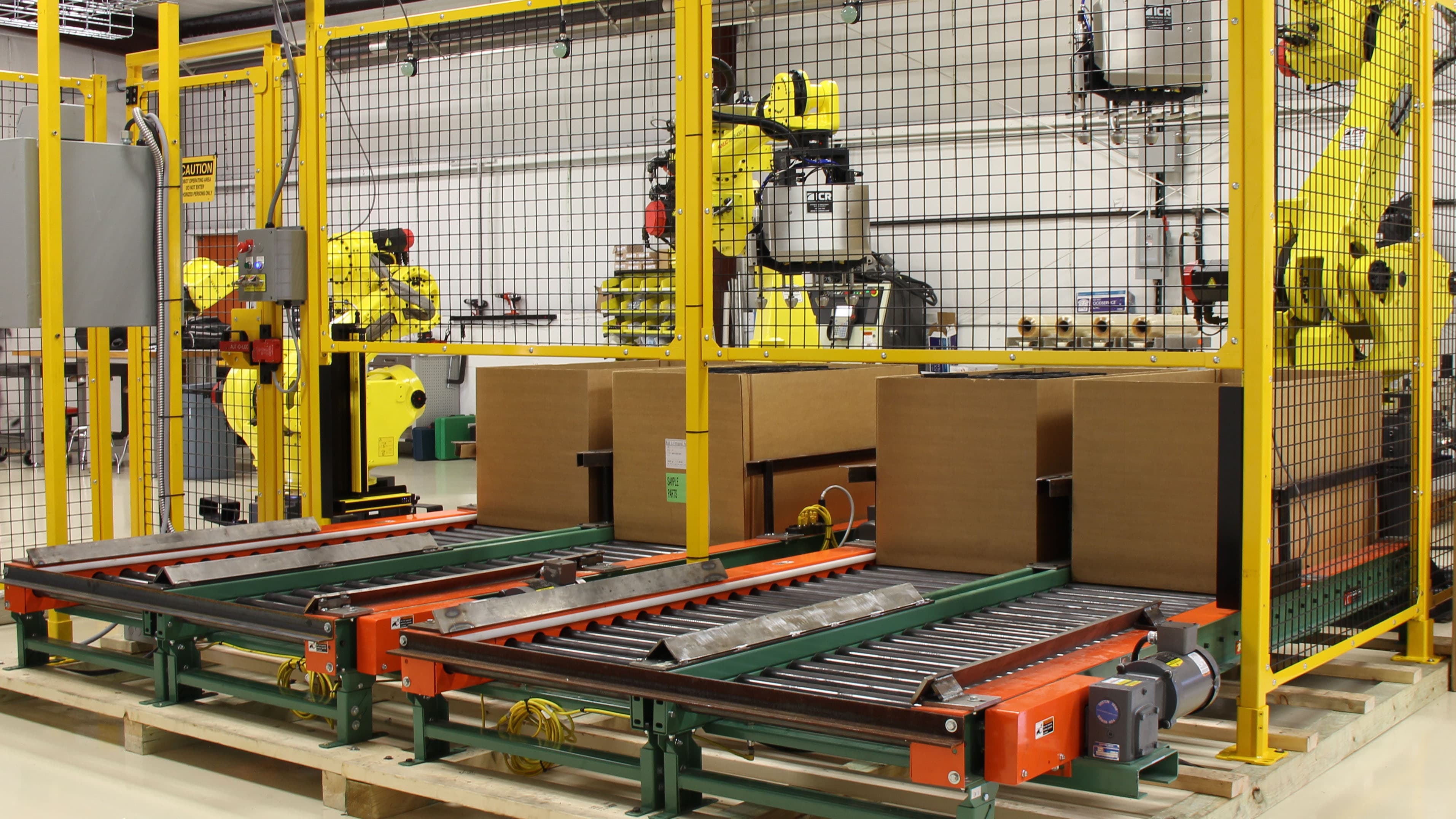
Warehouse Automation
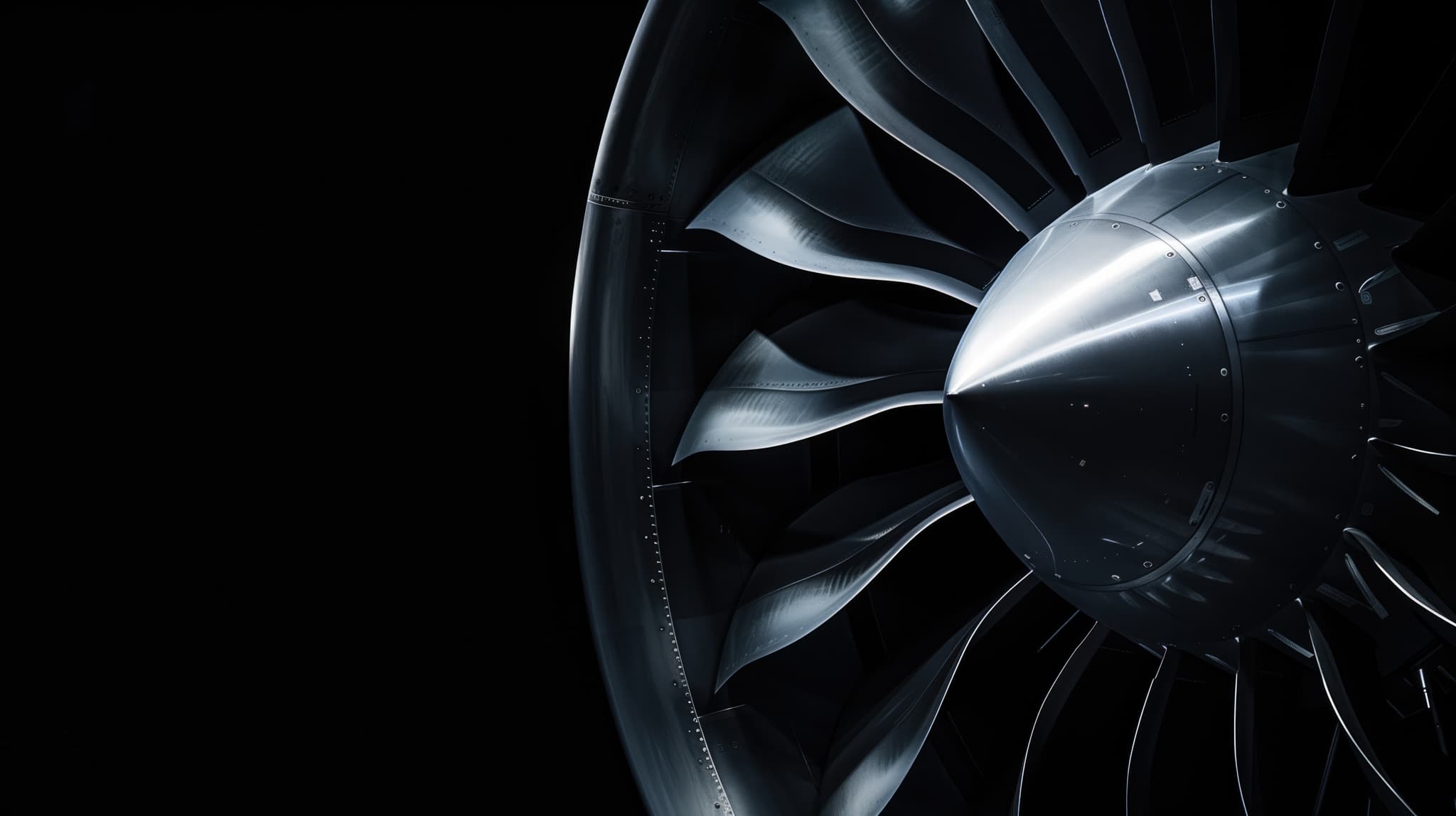
Aerospace
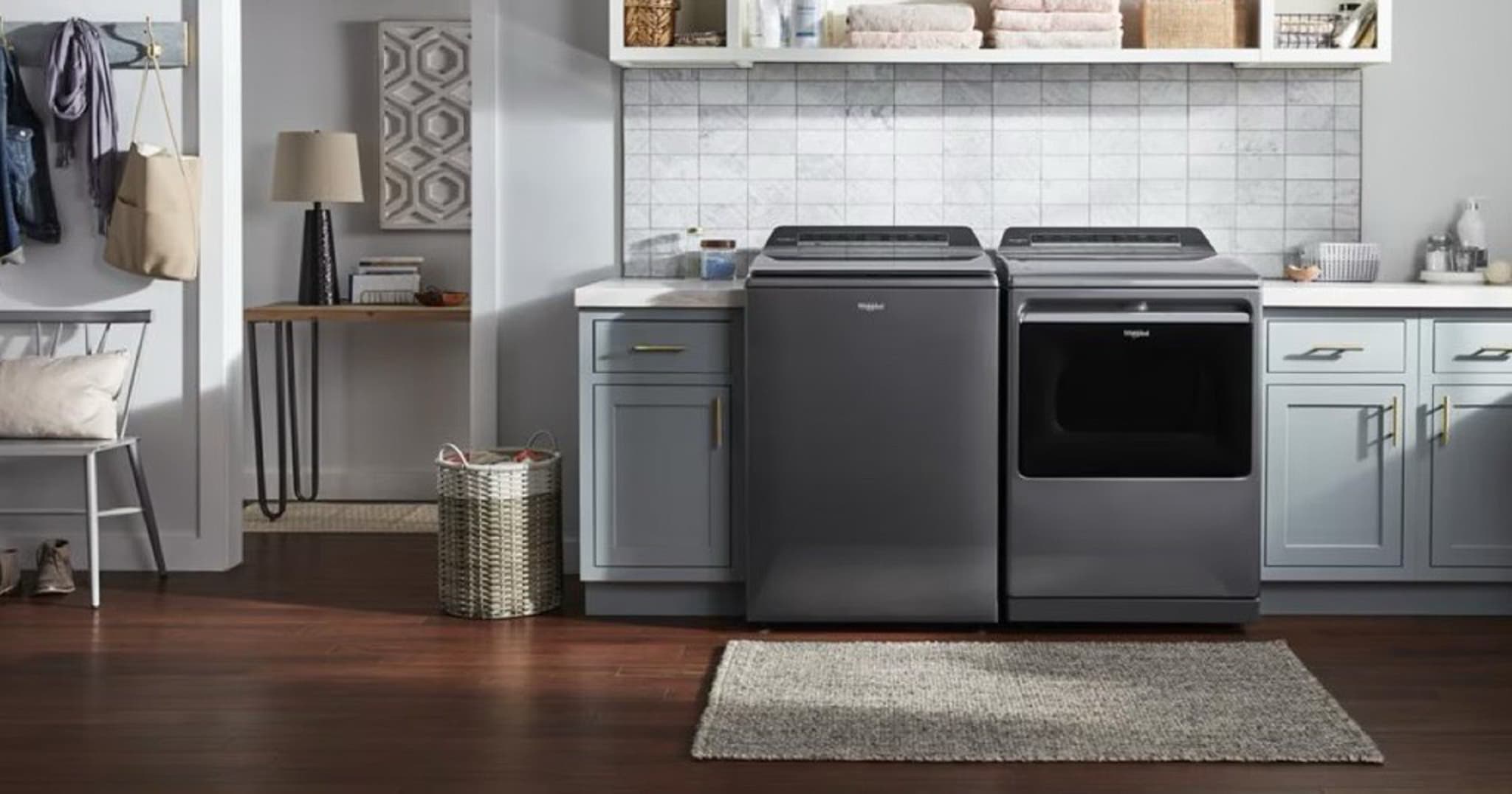
Consumer Goods
CS-421 Success Story
Replace manual operation with automated QC checks for burr-prone parts before pack-out.



Use a FANUC LR-Mate 200iD robot with iRVision above the infeed conveyor. A pre-check Touch Skip rejects oversized parts and moves to rework.
If the part fits the inspection station, the robot lifts it from the bottom, captures an image for rotation offset, and performs a quality inspection with 2-micron tolerance.
Total Cost of Ownership (TCO)
Purchase price only accounts for 15-25% of TCO.

CS-307 Success Story
Use KEYENCE VS AI-powered vision system to make pass/fail decisions on torque nut installation and upload images to FTP for archival.

CS-442 Success Story
A CRX-10iA cobot with iRVision moves parts from the infeed conveyor to a Fanuc ROBODRILL, sets the workpiece with correct orientation and alignment, and achieves a 2-micron tolerance.