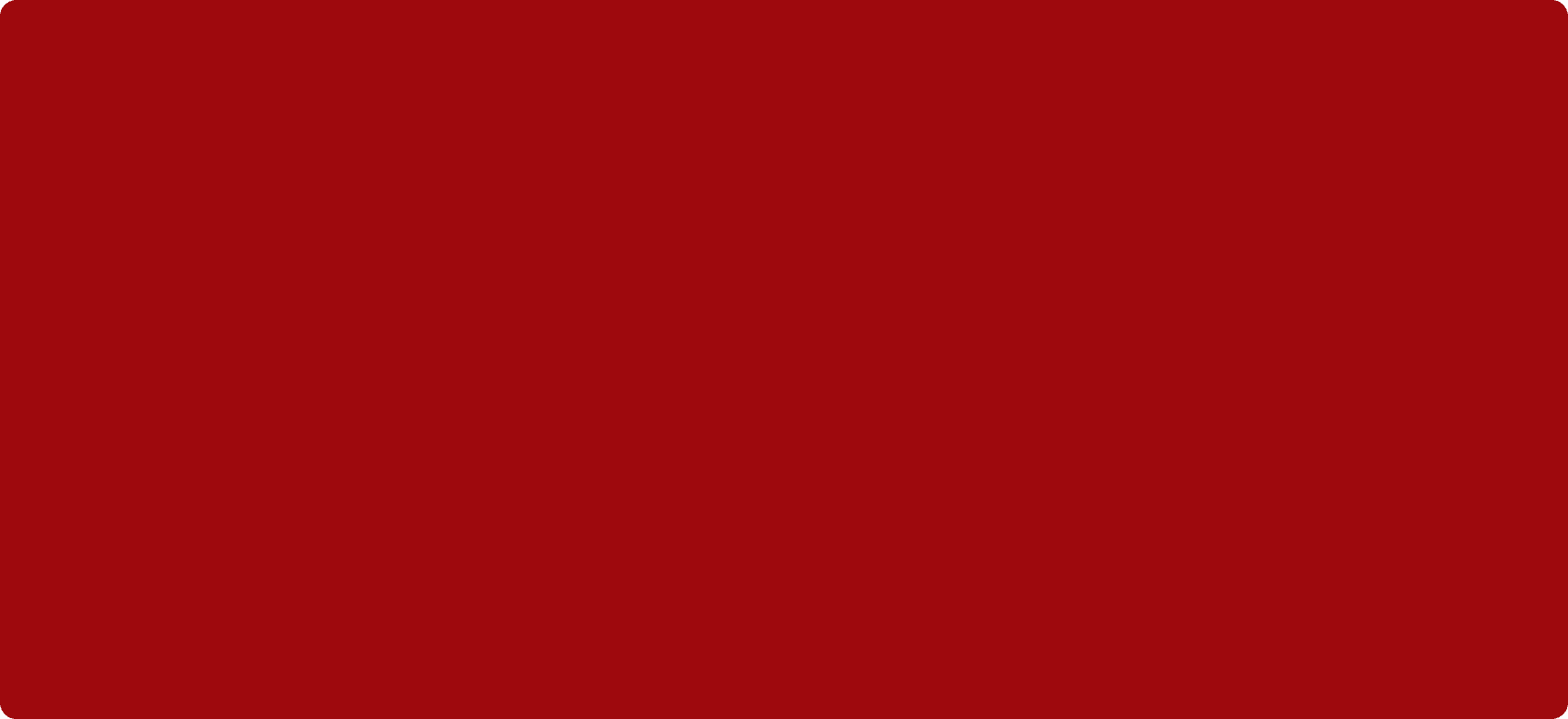
Field Service
Contract, Break-fix, and Scheduled Maintenance
Skilled, Safety-conscious Field Service Engineers
ICR is available 24/7, 365 days a year, with a 99% first-time fix rate.
- Well-rounded in mechanical and electronics
- Service many OEMs, not just one or a few
- Capable troubleshooters and programmers



Condition-based
Health Assessments
Identify issues using oil/grease analysis and inspection.

Break-fix
Corrective Maintenance
Quick scheduling and dispatch to resolve breakdowns and emergencies.

Planned
Preventive Maintenance
Prevent downtime with scheduled, routine maintenance.
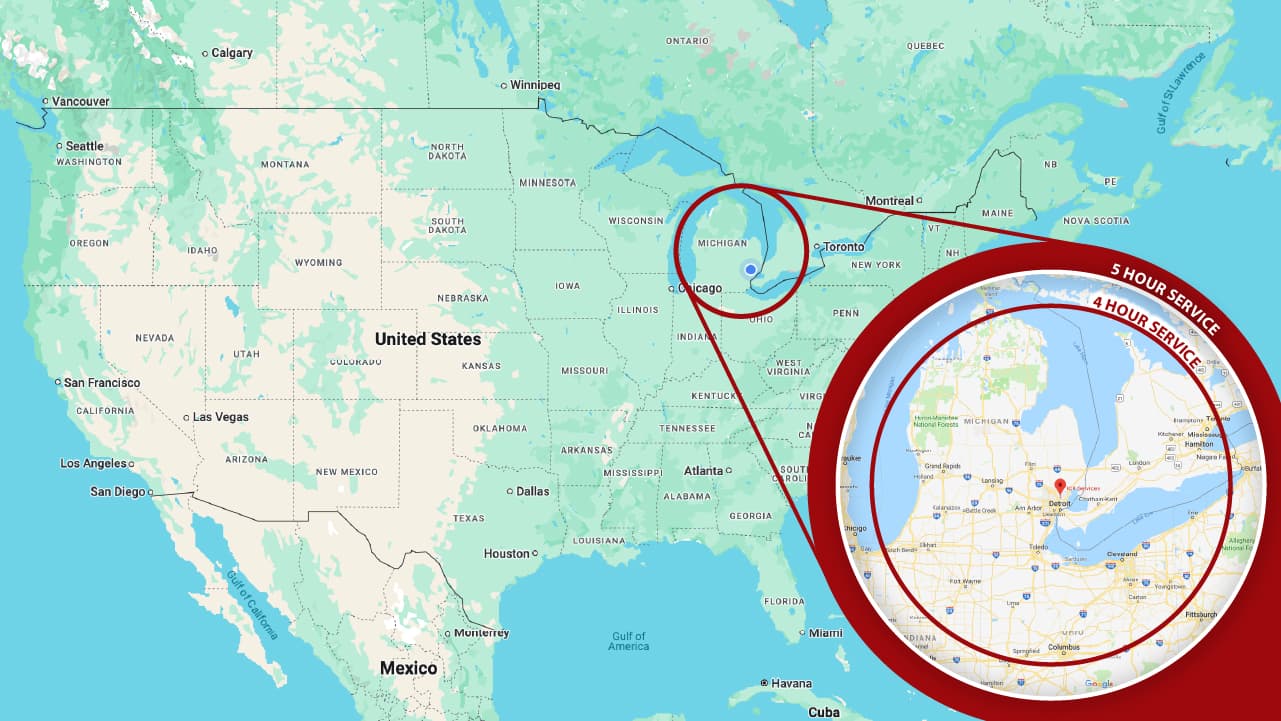
On-site
Nationwide Emergency Repair
Average Response Time: 4-5 hours across Michigan, Ohio, Indiana, and Ontario
Call for Details if Outside this Area

Systematic Approach
Troubleshooting
- PLC Troubleshooting
- Robot Troubleshooting
- CNC Troubleshooting

Well-tested, clean code
Programming
- PLC Programming
- Robot Programming
- CNC Programming
Schedule a Service Request
On-site Services
Continuously trained in best practices.

First-pass Yield
Process Improvements
Build ergonomic, lean processes.

CapEx Projects
Install, Commission, & Start-up
On schedule and within budget.

Workforce Development
On-site Robot Training
Essential upskilling and reskilling.
FAQs