Five benefits of effective spare parts management system
Maintaining a consistent production cycle is imperative for manufacturers with interruptions to the process proving to be costly. While processes are essential to maintaining consistency and production levels, industrial equipment can be both tricky and tough to repair or replace. As we mentioned, downtime is costly and, therefore, crucial to avoid. Sourcing equipment and implementing an adequate spare parts management strategy and abiding by preventive measures is necessary to maintain consistency.
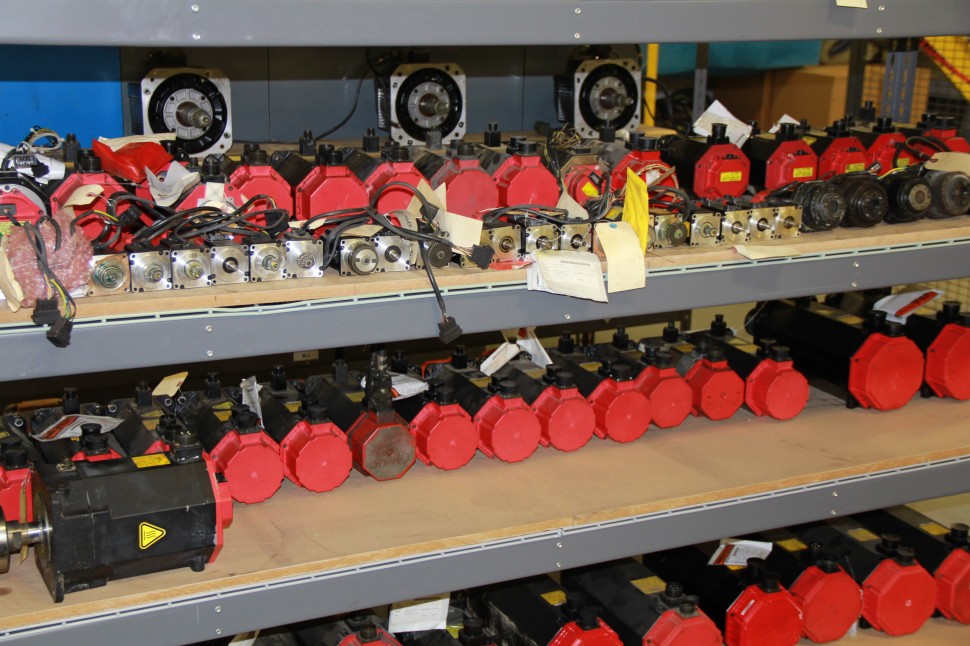
Minimized production downtime
Our on-site repair management division supports our customers with manufacturing facilities and operates within a predictive maintenance structure. Data collected from everyday operations, audits and survey’s power deep analysis and solutions to eradicate any issues. ICR staffed at our managed plant sites work hand in hand with their team developing solutions to avoid downtime.

Cost Reduction
Back at ICR’s headquarters in Warren, Michigan, our centralized purchasing team offers support through surplus industrial automation parts acquisition. These items are essential for controlling production processes at manufacturing plants without any shutdowns due to equipment malfunction. ICR’s ability to secure crucial surplus items proves cost-effective. Another advantage comes into play when OEMs no longer manufacture critical parts, plus a lower overall cost.

Established preventive measures
The processes at play within ICR’s on-site repair management service operate from within the core of Industrial Automation. To gain a better understanding of this concept is crucial to manufacturing operations a comparison to a NASCAR race is beneficial. Drivers need to navigate a course or track as efficiently and effectively as possible racing against time while avoiding potential pitfalls like equipment on their vehicle breaking down or colliding with other drivers on the racetrack.

Increased productivity
With automation equipment, when something breaks, the analysis needs to be conducted quickly to repair or replace the non-working equipment on a production line. Most issues resolve themselves through a repair or replacement parts. With the right planning and partner, surplus parts could be at the ready when issues occur. It’s important to note that downtime is an avoidable situation. With preventive steps followed production can remain active and running efficiently.
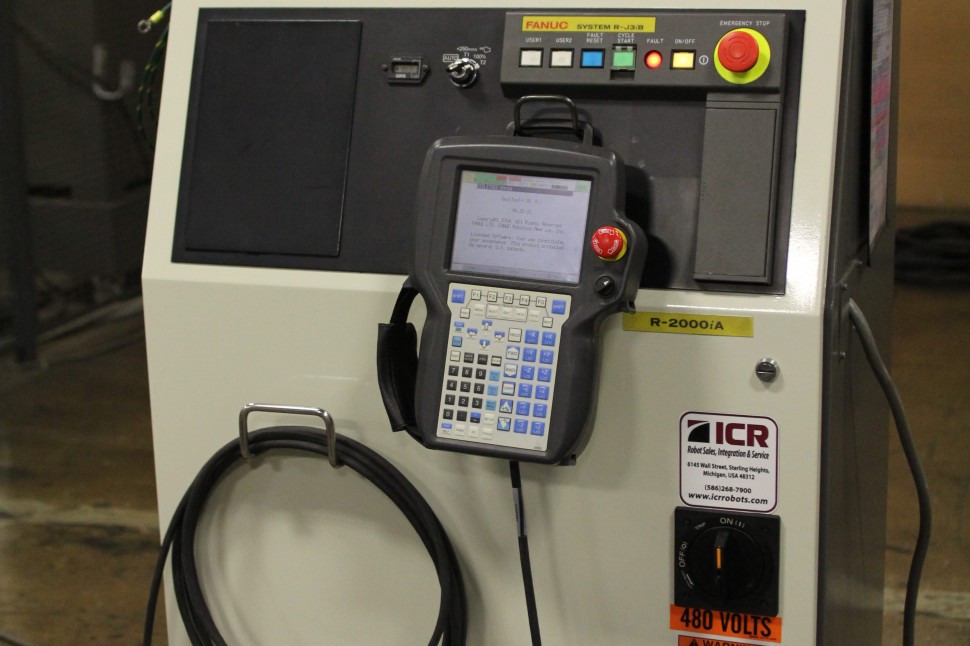
Reduced impulsive buying
As we pointed out earlier in this article, downtime is a costly endeavor. A potential revenue loss is apparent, but both labor and inventory issues can also crop up due to production downtime. Beyond lost revenue, there is also a high probability of customer fines, penalties or a canceled contract. ICR supports customers with surplus needs via our online store or through our internal network of support from our on-site repair management division.
