Manufacturing facilities need preventative maintenance
Within an industrial factory setting, unexpected breakdowns, and premature equipment failure can occur along any of the production lines or robotic cells as the massive amount of industrial equipment in use needs to operate smoothly. Avoiding any possible risk of failure is imperative for any manufacturing facility. When downtime hits production lines costs and loss of potential revenue become an issue quickly. Exploring the addition of preventive maintenance programs to equipment at your facility should occur before it’s too late.
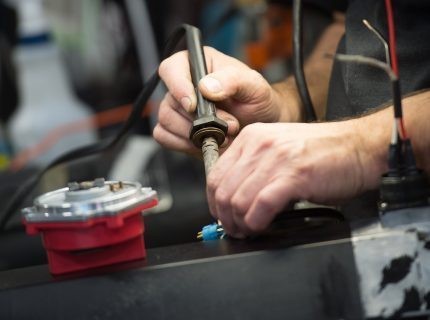
How PM helps the manufacturing process
In the repair business since 1992, ICR advocates preventive maintenance to its customer base during every interaction. When developing programs for a variety of equipment, ICR focuses on cost savings and adequate turn-around times for our customers. Research has indicated time and again that it is always more cost-effective to prevent breakdowns then it is to fix them. There are many benefits when adding a program for your industrial equipment. Adding PM programs provides immense value with a focus on elimination of potential machine downtime. This vital benefit offers a host of savings in the form of labor and capital cost expenditures.
PM Benefits
- Mitigate wear and tear on equipment by keeping it clean and lubricated
- Detect potential machine/part failures early
- Schedule full repairs instead of performing a partial repair
- Reduce maintenance and repair costs by eliminating emergency repair services
Reliability and longevity
AutomationWorld wrote about the need preventive maintenance back in 2012. Back then, the publication mentioned that “Bottom line, integrating preventive maintenance into enterprise management avoids costly repairs and interruptions and reinforces the facility’s reputation for reliable delivery.” As a verifiable source on industrial automation, the need for integrating a preventive maintenance program within factory environments has been validated.
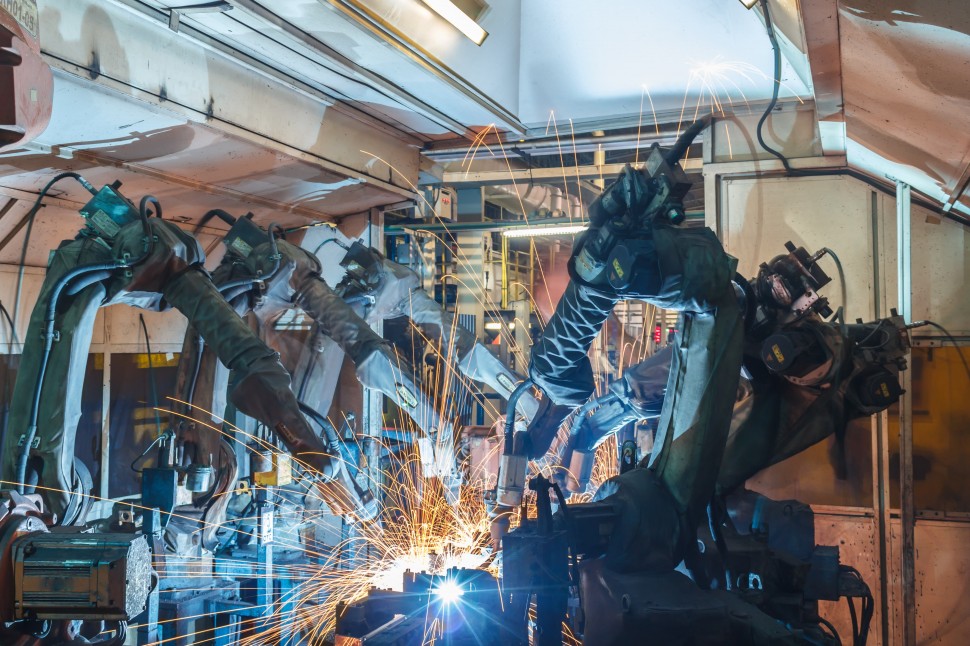