The main difference between an AC servo motor and a DC servo motor comes down to how electricity works. DC or direct current has both a positive and a negative terminal, with the current flowing in the same direction between each terminal. AC or alternating electric current operates in reverse, where the current alternates 50 or 60 times per second, depending upon the region.
AC has a slight advantage over DC as this type of electrical current handles changing the voltage of power much easier. AC does this by using a device called a transformer. The transformer allows power to flow a high voltage and still travel over long distances.
Now that we have the basics of electrical current down, how do the two different types of current work within a servo motor?
DC Servo Motor
- Brushes are within the motor
- Brushes wear and need replacement
- Preventive maintenance recommended
- Current moves through coils which sequences by the brushes and the commutator
- Control is much simpler than AC
- Field or current armature magnitudes are the only requirements for motor control
- A duty-cycle-controlled PWM operates motor speed
- Torque is controlled independently by a control flux, which allows the torque to maintain consistency while in operation.
- Inertia may reach a higher level in some situations
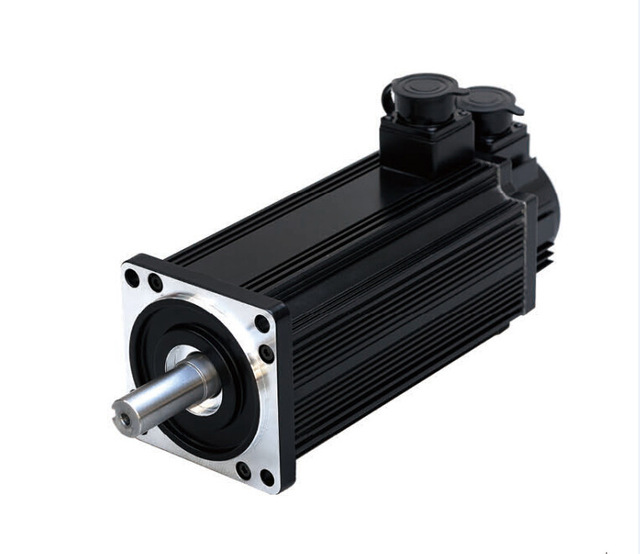
AC Servo Motor
- Brushes are not within the motor
- Less maintenance
- A feedback system controls and alerts the engine to the location of the rotor to initiate the sequence of current through the coils.
- Feedback alignment is used within most AC servo motors to function properly with a controller or amplifier.
- Inertia is lower on rotors
- Sophisticated control system
- Stator current magnitudes, frequencies, and their phases require a coordinated control process.
- Closed-loop communication system located with the controller/amplifier
- Motor speed operates by a sinusoidal PWM, where the speed control is in the frequency of the PWM
- Higher RPM with the ability to reach 6000 RPM on many servo motors
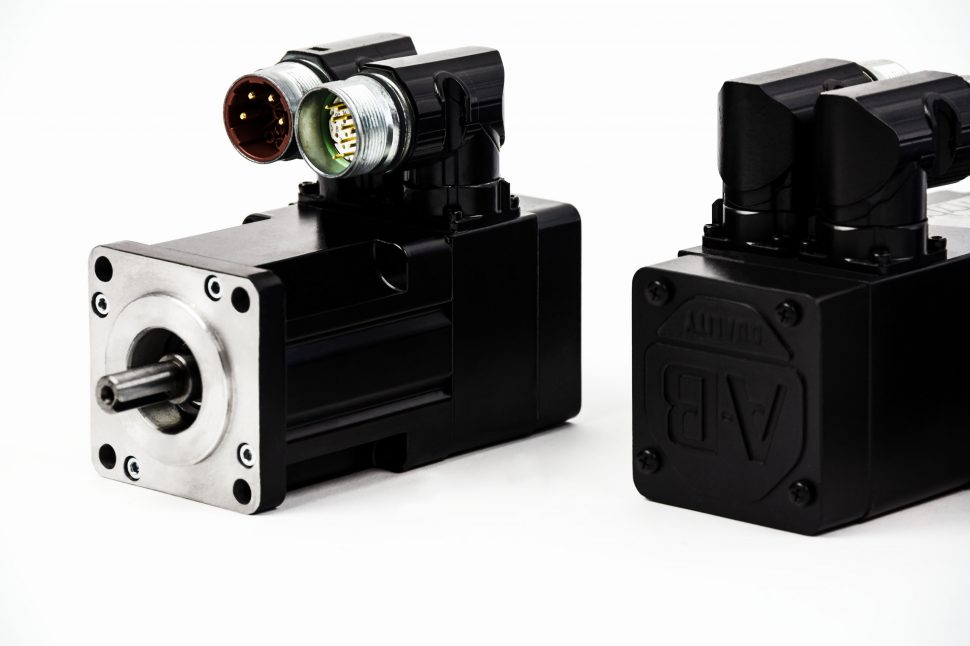
Benefits of Servo Motor Preventative Maintenance
ICR recommends preventive maintenance on any and all servo motors in production. ICR’s refurbishment process operates from a predictive maintenance mindset, applying preventive measures to ensure reliability and logevity. Technicians will provide support from our field service division on-site or at our repair facilities.
Preventive maintenance programs bring servo motors back to OEM set specifications or greater. Whether a program is needed or a quick repair ICR is the resource to provide the support needed. Request a mechanical repair quote for your motors when issues creep up.
Motor Testing
- Sensor testing and alignment
- Holding brake test
- ICR’s in-house brake refurbishment provides a brand-new brake assembly
- Vibration analysis
- Dyno testing
*ICR Services is not an authorized Rockwell Automation distributor or repair company in any way affiliated with Rockwell Automation. ICRServices.com is not an authorized distributor, affiliate, or representative for the listed manufacturers unless explicitly stated otherwise. Designated trademarks, brand names and brands appearing herein are the property of their respective owners.