An Informative Guide by Andrew Valentine – Training Instructor, ICR services
5 Proven Practices to Implement Before Robot Downtime Strikes
Unexpected robot downtime or component failures occur quite frequently with each line down scenario costing upwards of $22,000 per minute. In the event the downtime results in the inability to deliver parts, your cost can easily exceed $50,000. How quickly the robot can be recovered will be determined by how well you’re prepared.
The following recommendations should be added to your robot preventative maintenance program as they guarantee a quick recovery with minimal disruption to production.
- Have a plan to assure up-to-date robot backups are made weekly
- Use PC cards instead of USB sticks for faster recovery
- Replace batteries as needed
- Verify robot witness marks are visible and still intact for each axis
- Document tool center points and encoder counts
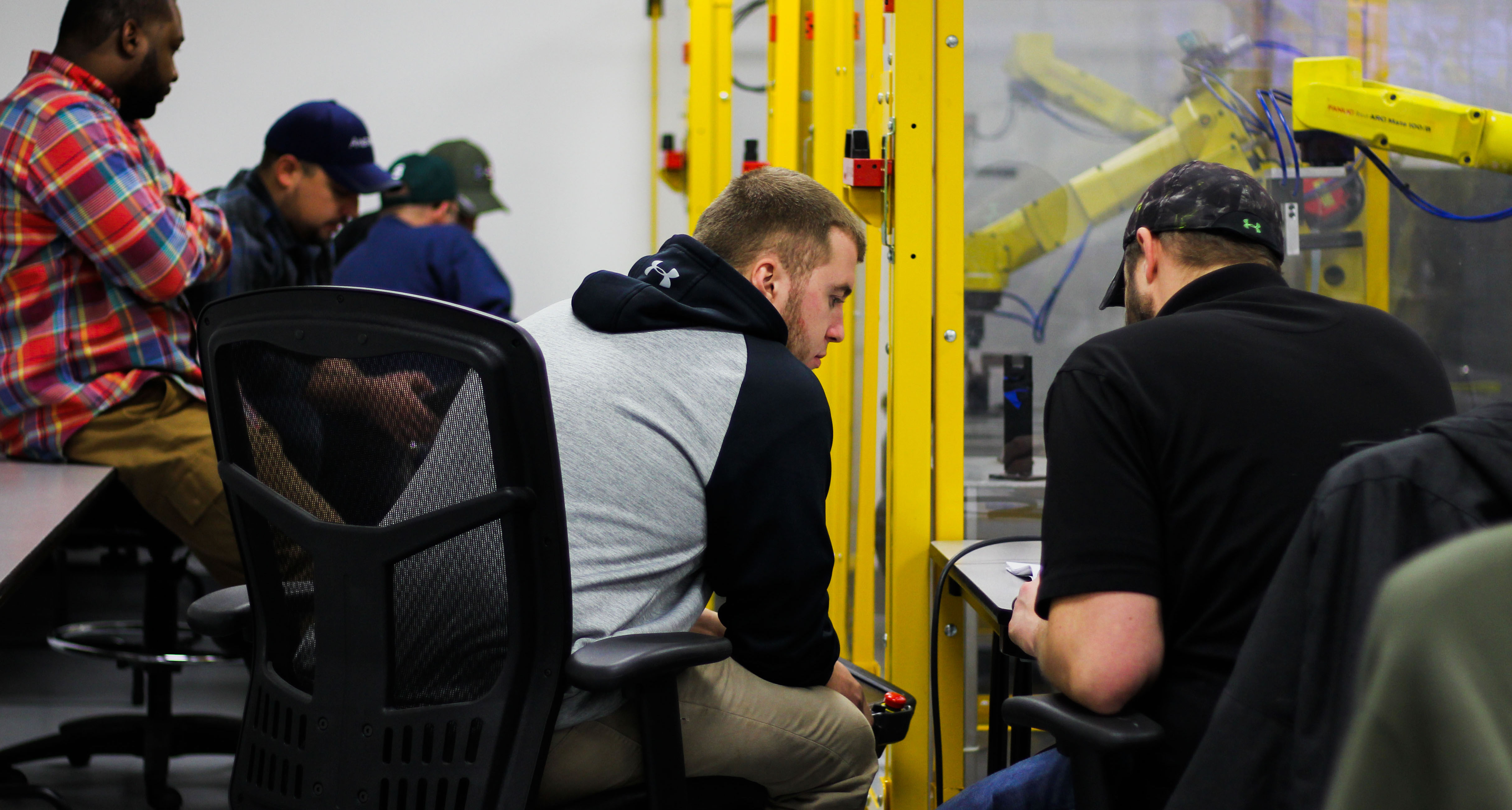
Recommendation 1: Perform Weekly Robot Backups
The most valuable item to have on hand during a downtime scenario is up-to-date backups. Not having them can be the difference in recovering in minutes vs. having the line down for days. Customers using Fanuc robots should make both types of backups for RJ3 series or newer: Standard Backups and Image Backups.
Having both types of backups available allows for selecting the most efficient way to recover the robot as each provides different options for recovery.
Standard Backups
The Standard Backup or All of the Above Backup saves each file individually.
Types of Files
Robot Program Files, System Configuration Files, System Variable Files, Register Files, Frames, TP & Macro Programs, etc.
Benefits
Allows for the loading of individual files back to the robot controller as needed. This is especially helpful for recovering recent program touch-ups or adjustments
Compatible Controllers
RJ to R-30iB
Image Backups
The Image Backup restores all files, plus the robot system software by taking a snapshot of the memory 1 MB at a time. This all-or-nothing approach reloads EVERYTHING.
Types of Files
All files & robot system software are saved
Benefits
An Image Backup can restore all files, plus the robot system software
Compatible Controllers
RJ3 and newer
Many large corporations have their robots communicating on a network so that scheduled backups can be uploaded directly to a server each week. Most small and midsize businesses that use older equipment do not have this capability and have no plan in place to perform robot backups regularly.
Not sure what to do? How to perform proper robot backups is one of many things discussed in our ABB and Fanuc Robot Training Courses.
Recommendation 2: Use PC Cards instead of Flash Drives
If you’re looking to speed up the backup or recovery process you’re best to go with a compact flash card with adapter instead of the more traditional USB method. Most can be purchased for under $20. This card is inserted into the control panel or main board for R30iA and R30iB controllers.
Image Restore Time USB vs PC Card
- PC Cards: 1-8 minutes
- USB Flash Drives: 4-25 minutes
Standard Backup Restore Time USB vs PC Card
- PC Cards: 1-5 minutes
- USB Flash Drive: 3-13 minutes
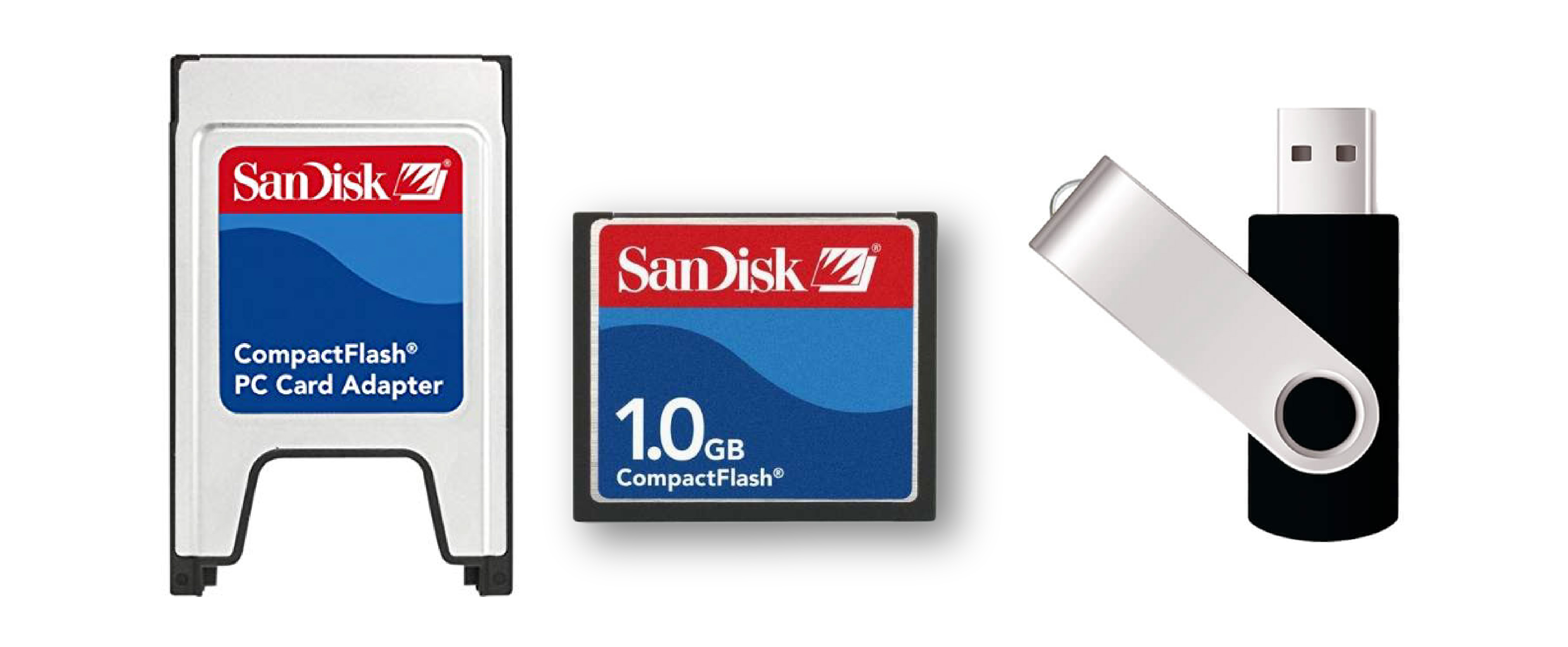
Recommendation 3: Replace Batteries Annually
Important: Always replace batteries with POWER ON. Removing batteries with power off will require either remastering of the robot or reloading the system software and all programs.
Every Fanuc Robot has (2) sets of backup batteries. (4) batteries are located on the arm and (1) in the controller on the main CPU board for a total of (5). If the robot has additional axes for servo guns, rails, turntables, etc. these will be additional batteries that need annual replacement.
The batteries on the robot arm must be replaced yearly. The needed type is normally (4) alkaline D or C cell batteries, whereas the lithium battery on the main CPU board – which maintains the robot memory – must be changed every 4 years.
Recommendation 4: Make Sure Witness Marks Are Visible
One-degree of misalignment on a major axis when remastering may throw off robot positions up to one inch.
The vulnerability of witness marks / mastering marks makes them susceptible to the environment. The foil stickers placed on larger Fanuc robots may fall off due to grease and oil contamination, while the scribe lines on smaller models easily get covered in dust and weld slag. Both situations make it very difficult to locate these marks once in operation.
Without witness marks, remastering the arm can be time consuming since there’s no visual way of knowing the proper axis alignment. If a single axis is off by a single degree, the encoder count may be ± 50,000 counts resulting in a need for further mastering – otherwise positions in the program would need to be touched up which can take days for path intensive programs with multiple part styles.
The fastest way to locate these marks is to add a Zero Program to the robot. This is position recorded so all motors and joints are aligned to zero degrees. While the robot is mastered – cycling to zero makes finding and marking each axis at the proper location fast and easy. Variations of a Zero Program may be required if moving to a zero would cause the robot to collide with other objects in the cell. Then several positions are used to verify axes are aligned properly.

Recommendation 5: Document Tool Center Points and Encoder Counts
Having a document with both Tool Center Point Values (TCP) and Encoder Counts can save you time depending on the robot issue.
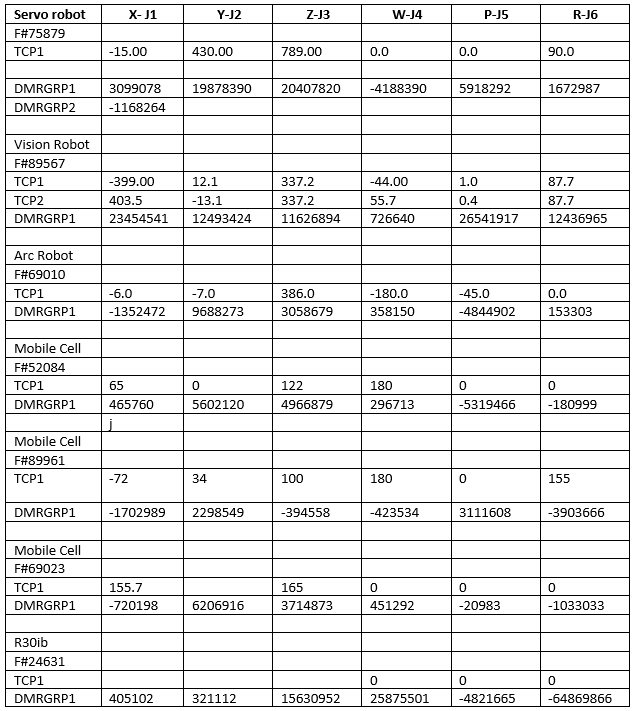
Where to Find this Information:
Encoder Counts can be found under: System Variables ► $DMR_GRP ► DMR_GRP_T ► MASTER_COUNT
Tool Center Point Values can be found under: Menus ► Setup ► Type ► Frames ► Other ► Tool Center Point.
The original paperwork provided by the manufacturer when you purchased the robot is another possible source. If this information is unavailable, create a document like the one above to reduce your recovery time by 50%. If you need to perform master or TCP setup, find an experienced robot programmer or maintenance technician and they should be able to manually re-enter this information in minutes.
There are times when encoder values can be re-entered instead of having to perform any remastering. This will save time since improper alignment during remastering may affect positions in the program.
Preparing the Next Generation of Maintenance Leaders and Engineers
ICR offers training to properly prepare our students on all of these methods. Proper and efficient robot recovery is critical to greatly reduce the amount of downtime when a component failure occurs.
Are you properly prepared for the next major robot downtime event? If not we can help!
About the Author
Andrew Valentine has developed training techniques curriculum on and copyrighted over 25 courses on PLC’s, robotics, and welding – including body shop, paint and final assembly applications. He graduated with a Bachelor of Science degree in Robotics in 1986. Andrew was a service and installation engineer at Fanuc NA from 1988-92. In 1996 Andrew and his wife Amy Valentine founded Valentine Robotics. Valentine Robotics trained over 8000 people from 1996-2009.
The curriculum Andrew originally developed has now trained over 20,000 students. Andrew sold Valentine Robotics in 2009 and has since partnered with companies to continue offering high quality robotics, controls, and welding technology courses using newly developed materials and methods. His goal being to help manufacturers prepare the next generation to operate and maintain automated systems and technologies.